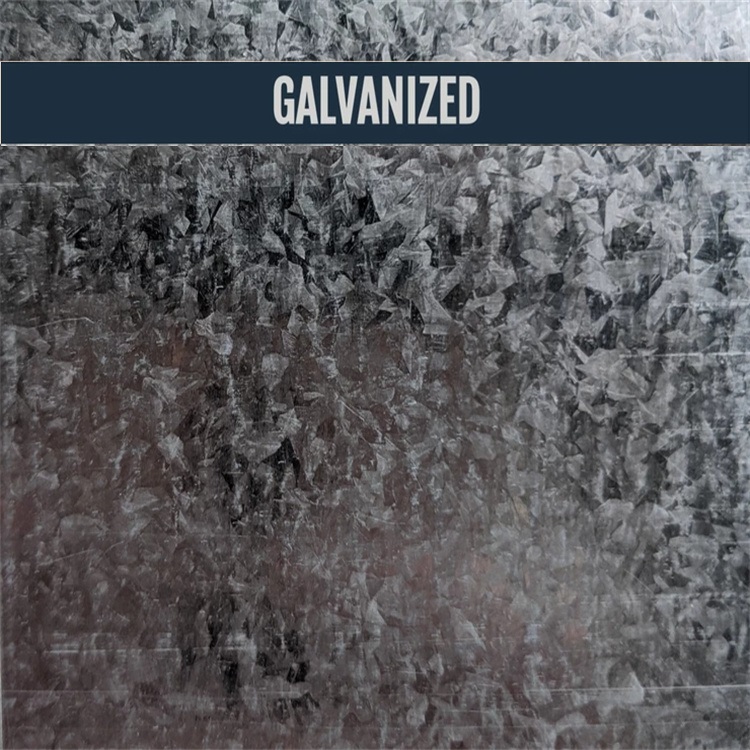
Galvanized steel (GI) is the first generation of coated steel. Its coating mainly contains Zinc over 99%. And it is currently the most widely used coating steel due to its longer history.
Galvanization is a protective zinc coating applied to a steel or iron substrate through a hot-dip galvanizedprocess. Pure zinc-coated steel is divided into two types: spangle-free and regular spangle, and their corrosion resistance is almost the same.
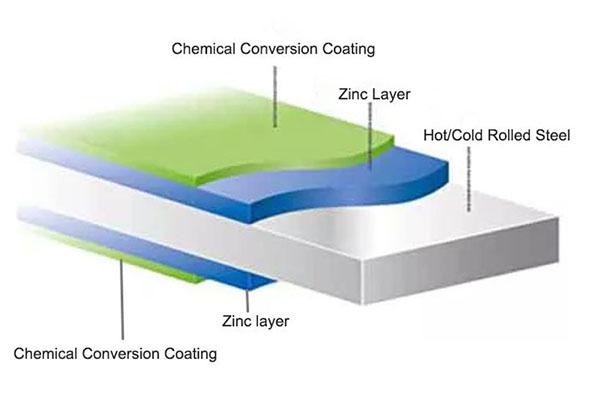
Surface Structure | Zero Spangle | Big Spangle |
Weight of zinc coating | Zinc > 20g/sm | Zinc > 30g/sm |
Surface Finish | ![]() | ![]() |
DISADVANTAGES
Red Rust
After the GI has been used for a period of time, galvanized steel starts from the oxidation of the zinc layer, which will form a layer of a gray-white powdery substance. That is called white rust. Then white rust further reacts with impurity gases such as carbon dioxide in humid air to form black spots, which is the so-called “black rust”. Over time, the zinc layer is corroded little by little. When the zinc layer is exhausted, the base metal loses the zinc protective layer and begins to oxidize, resulting in “red rust”. Once “red rust” occurs, the corrosion will become very fast. Until the substrate is rusted, the galvanized steel will end its service life.
Welding Joint Rust
Welding point areas become the most vulnerable to corrosion as the protective zinc layer is easily compromised due to zinc coating deteriorates, the underlying steel is exposed to these corrosive agents, leading to corrosion. It should be noted that if rust occurs at a certain point of the GI pipe, if timely measures are not taken, the rusted area will gradually become larger and larger and eventually even the entire pipe.